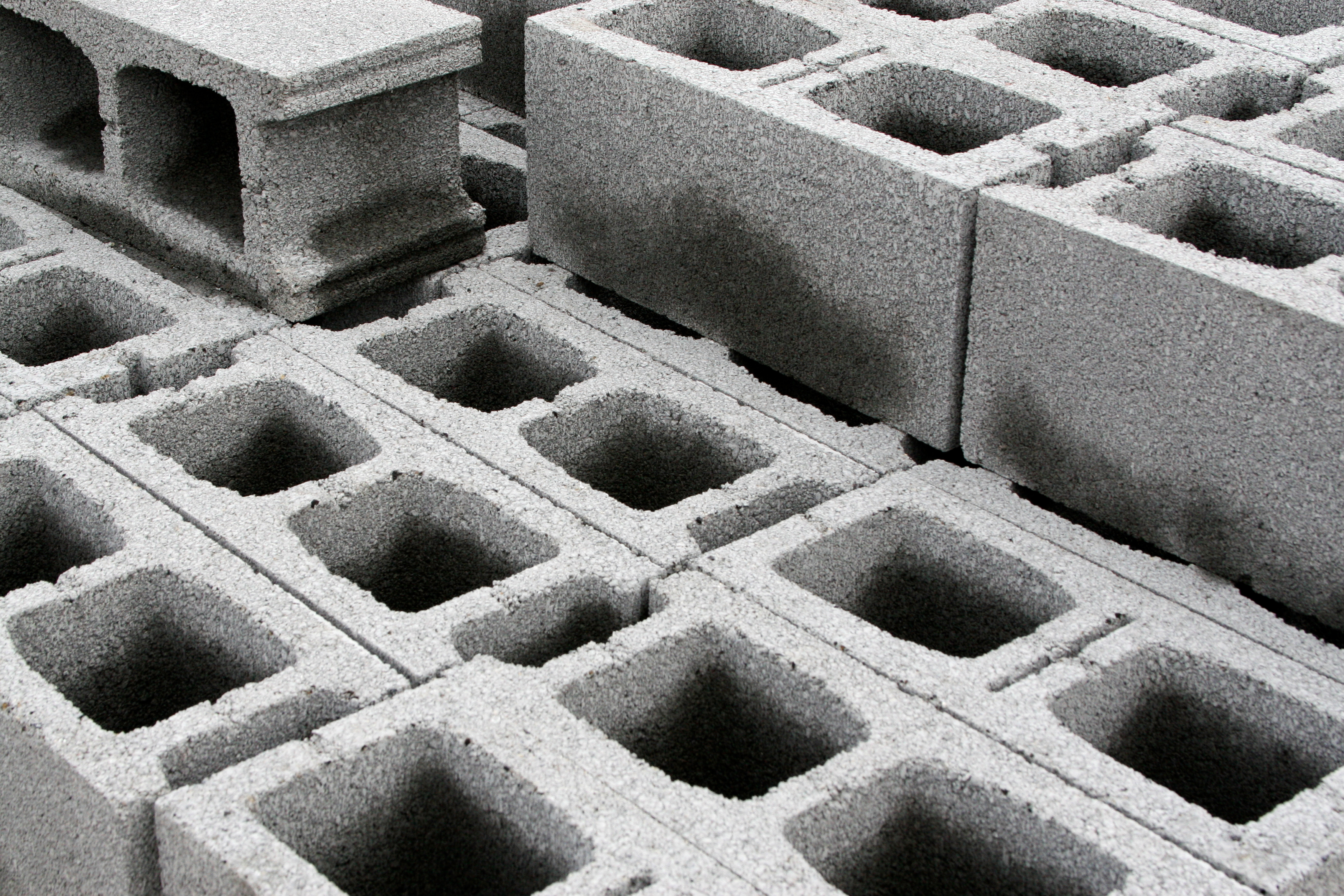
Concrete block manufacturing involves distinct phases that ensure the production of high-quality blocks for construction purposes. Each phase plays a crucial role in shaping the final product.
Preparing Raw Materials
1. Gathering Ingredients:
- Cement
- Aggregates, such as sand, gravel, or crushed stone
- Water
- Optional admixtures for enhanced performance
2. Mixing Ratios:
- The general mix ratio consists of 1 part cement, 2 parts sand, and 3 parts aggregate.
- A calculated quantity of water activates the cement hydration process.
Moulding
1. Moulding Process:
- The concrete mix gets poured into a mould box.
- Compaction systems shape the concrete, ensuring it fits the desired dimensions.
Curing
1. Curing Process:
- Blocks remain in a controlled environment to harden effectively.
- Maintaining moisture during the curing phase is vital for proper cement hydration, which lasts from 7 to 28 days.
2. Manual Method:
- The manual method is simple and cost-effective.
- This approach lacks vibration and high pressure, generally leading to blocks of lower quality.
3. Automated Method:
- Automated systems improve precision and efficiency.
- This method produces consistent quality due to controlled conditions and advanced machinery, such as those offered by block machine manufacturer Lontto.
Understanding these manufacturing phases equips stakeholders to improve production quality and optimize processes.
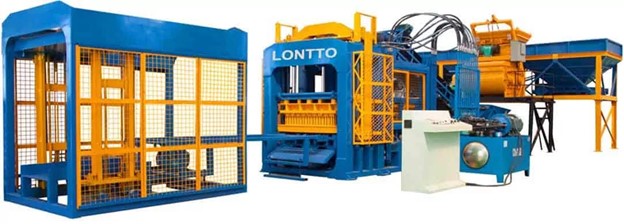
Materials Required
Manufacturing concrete blocks requires several essential materials that contribute to their strength and durability.
Cement
Cement serves as the primary binding agent in concrete block production. Portland cement is the most commonly used type, available in powdered form. When mixed with water, it forms a paste that effectively binds aggregates together. This binding is crucial for achieving the structural integrity of concrete blocks.
Aggregates
Aggregates play a significant role in providing strength and bulk to concrete blocks. Common types include:
- Sand: Fills voids and improves workability.
- Gravel and Crushed Stone: Offer compressive strength and stability.
- Limestone: Enhances durability and is cost-effective.
- Clay and Shale: Provide additional plasticity and strength.
Other aggregates like shells, chalk, marl, slate, blast furnace slag, silica sand, and iron ore may also be used, depending on local availability and desired properties of the finished product.
Additives
Additives are optional materials that improve specific characteristics of concrete blocks. These may include:
- Chemical Admixtures: Improve workability, accelerate curing, or increase water resistance.
- Nanoparticles: Improve durability and strength at the microscopic level.
- Nanofibers: Improve toughness and flexibility.
Incorporating additives can optimize the performance of concrete blocks to meet various construction needs.
Manufacturing Process
The manufacturing process for concrete blocks consists of three key phases: mixing, molding, and curing. Each phase plays a crucial role in producing high-quality concrete blocks.
Mixing
- Raw Materials: The process starts with procuring raw materials, including cement, aggregates (sand, gravel, or crushed stone), water, and optional admixtures to modify the concrete's properties.
- Mixing Ratio: A common mixing ratio is 1:2:3, which comprises 1 part cement, 2 parts sand, and 3 parts aggregate. A precise amount of water acts as a catalyst, facilitating the cement's binding qualities.
- Blending: A stationary mixer blends the ingredients for several minutes. This blending may include planetary or pan mixers. During this phase, water and any admixtures or dyes are added to achieve the desired consistency and color.
Molding
- Mold Preparation: After blending, the concrete mixture transfers from an incline conveyor to a mold box fitted with multiple mold liners.
- Filling Molds: The mixed concrete is then loaded into the molds, ensuring even distribution to achieve the desired dimensions of the blocks.
- Compaction: The filled molds undergo compaction using vibration or pressure to eliminate air voids and improve density. Proper compaction results in stronger and more durable concrete blocks.
- Curing Techniques: Curing follows molding and involves maintaining moisture to facilitate the hardening process. Techniques include water spraying, soaking, or covering with wet burlap.
- Duration: Curing typically lasts from 7 to 28 days, depending on environmental conditions and the desired strength of the concrete blocks.
- Quality Control: Regular monitoring during the curing phase ensures optimal conditions. Proper curing prevents cracking and improves the final product's mechanical properties.
Quality Control Measures
Quality control measures ensure that concrete blocks meet established standards for strength and durability. These protocols involve systematic procedures and assessments throughout the manufacturing process to identify and rectify issues.
Testing Methods
Testing methods play a crucial role in validating the integrity of concrete blocks. Common tests include:
- Compression Tests: These measure the ability of the block to withstand axial loads, ensuring adequate structural capacity. Blocks are subjected to pressure using hydraulic machines until failure occurs.
- Water Absorption Tests: These assess the block's porosity, which affects durability. By submerging the block in water and measuring the weight before and after, manufacturers determine its water absorption rate.
- Dimensional Checks: These verify that each block conforms to specified dimensions. Measurements ensure consistency in size, which impacts stacking and alignment during construction.
Common Defects
Common defects in concrete blocks can lead to compromised quality. Recognizing these defects ensures timely remediation. Key defects include:
- Cracks: Surface or internal cracks can weaken the block and are often caused by improper curing or excessive compression during molding.
- Air Bubbles: Air pockets may form within the concrete, affecting its strength and insulation properties. These occur due to inadequate mixing or vibration methods.
- Dimensional Variations: Inconsistent sizes can create challenges in construction. Variations often result from uneven filling of molds or errors in material batching.
Implementing rigorous quality control measures and regular testing enhances the reliability of concrete blocks in construction applications.
Environmental Considerations
Manufacturing concrete blocks involves several environmental challenges that require attention. The following factors highlight significant considerations.
- Cement Production: Cement production contributes roughly 8% of global CO2 emissions. This impact emerges from the process itself, necessitating measures to reduce emissions during cement manufacturing.
- Raw Materials: Extracting raw materials like limestone, clay, and sand can destroy habitats and deplete local resources. Sustainable sourcing practices mitigate these effects by ensuring minimal ecological disruption.
- Energy Consumption: Significant energy is necessary for the concrete manufacturing process. Often, this energy comes from fossil fuels, raising emissions. Implementing energy-efficient practices and exploring renewable energy sources can help reduce the carbon footprint.
- Water Usage: Large quantities of water are necessary for producing concrete. This demand can strain local water resources, especially in arid regions. Utilizing water-saving technologies can alleviate pressure on these vital resources.
- Waste Generation: The manufacturing process generates waste, including dust and other by-products. These materials can pollute the environment if not managed properly. Adopting waste management strategies can minimize environmental impact and promote recycling of materials.
Conclusion
Mastering the art of concrete block manufacturing requires a blend of technical knowledge and sustainable practices. By focusing on quality control and understanding the environmental impact of the production process, manufacturers can produce durable blocks while minimizing ecological footprints. Embracing innovative techniques and efficient resource management not only enhances product quality but also aligns with growing sustainability demands. As the industry evolves, staying informed about best practices will ensure a competitive edge and contribute positively to the environment.