Matthew Aladesaye is a PhD qualified Mechanical Engineer from Massey University, Auckland, New Zealand with experience in Reliability, Condition Monitoring, Research & Development, and Machine Design. In the following article, Matthew Aladesaye takes a look at the different strategies that are utilized in mechanical engineering and how they can be applied to business to achieve success.
Businesses unable to adapt are rarely successful. That’s especially true when a company’s work requires efficient and reliable
mechanical engineering processes.
Matthew Aladesaye explains that the automotive industry would not have grown without a refined assembly line process and essential internal combustion engines. Electricity would not have taken hold without powerful generators.
With consumer needs ever-changing and technology evolving at a breakneck pace, it’s the mechanical engineering processes themselves that are in constant need of improvement. Whether it’s small tweaks or massive overhauls, new strategies to improve these methods are in constant demand.
While such strategies are never one size fits all, here’s a look at several that have proven effective across various industries.
Going Step by Step to Find the Issue
It’s not enough to know that there is a problem within the engineering process. Businesses must dig deeper and that often means pinpointing exactly where the process stalls to work on its efficiency.
A team approach works best to find the bottlenecks and determine the lost value without improvements. Matthew Aladesaye says that there’s often a step or a machine that takes up the largest capacity percentage or takes the longest to complete a task. Both would be considered bottlenecks.
Industrial engineer Taiichi Ohno once outlined seven waste types often found in manufacturing, including overproduction waste, material movement waste and waste of waiting.
Using a methodology called value stream mapping (VSM), a molded case circuit breaker manufacturer in Vadodara, India, took a hard look at its assembly flow and reduced the lead time needed for production while increasing value.
Matthew Aladesaye reports that finding the areas containing the largest amount of backlogged work reflects faulty or outdated engineering. Modernizing processes, especially those most valuable leads to improved technologies and a drastic overhaul of efficiency. By combining optimization with improvement, businesses can quickly improve the assembly line.
Target Shipping
Efficiency improvement strategies can also be implemented in a company’s shipping process. While materials related to shipping are often far less expensive than engineering and manufacturing tools, the cost of shipping tends to accumulate quickly.
Oklahoma City-based oil and gas company Kimray decided to take a look at its shipping process, make a few adjustments, and cut costs related to shipping pads by half.
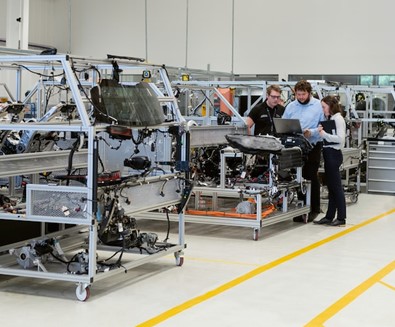
Go Lean
A specific strategy to improve engineering processes has proven particularly effective over the years. Matthew Aladesaye explains that an approach called the Lean Six Sigma (LSS) has been used to improve not just the quality of products but reduce associated waste and refine the efficiency of operations.
VSM is just one tool within LSS and it’s the totality of the strategy that makes a real difference. One 2022 study found that by using LSS techniques, the assembly process for a railroad truck improved the process cycle efficiency by
nearly 47% and lead to a value increase of over 59%.
The LSS system was first developed in the 1940s to generally streamline manufacturing, mainly focusing on
ways to decrease waste while enhancing process flow.
Matthew Aladesaye says that the steps include outlining a specific problem, measuring how impactful the problem is, looking for the problem’s cause, experimenting and locating the best improvement technique and then maintaining the improvement and its result.
Embrace New Technology
The development of 3D scanning and printing has been a boon for the manufacturing industry by creating 3D models of work sites, tools, and assembly lines. The resulting data can do everything from improving day-to-day safety and predict future management process risks.
Such scanning, offered by process improvement consultant companies is increasingly popular amongst companies prioritizing overall productivity improvement. They can provide a digital blueprint of combustion systems and the design of equipment, as well as help with process expansion goals.
Matthew Aladesaye says that these 3D scans can also be used down the road when a company decides to expand — scans may be used to create duplicate systems that are equally efficient — or if they simply wish to maintain their processes efficiently.
3D scanning accuracy is beneficial in many ways. Specific mechanical engineering tools can also be easily identified when a company seeks the bottlenecks that disrupt production.
For example, the water industry may use such modern technology to make minor but essential tweaks to the mechanical engineering processes needed to reduce the overall wastewater pretreatment phase. That may help a company save millions of dollars each day.